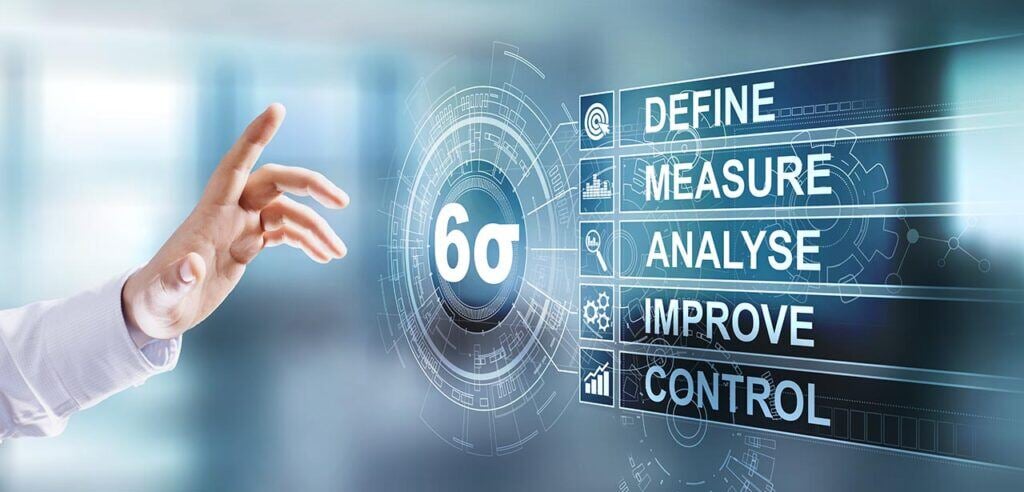
Creating a culture of Continuous Improvement
Continuous improvement ensures that organisations and processes not only continue to function optimally, but can also respond effectively to change.
Continuous Improvement
The key to an agile and future-proof organisation
In a constantly changing world with new laws and regulations, ever-increasing expectations, and the pressure to work more efficiently, continuous improvement is essential for organisations and local governments. But what exactly does continuous improvement entail? Why is it so important, and how can it be applied effectively within an organisation?
What is continuous improvement?
Continuous improvement is about continuously increasing operational efficiency and the quality of services and products. This approach, inspired by methodologies such as ‘Kaizen’ and Lean principles, focuses on continuous, iterative and small improvements that collectively have a large and lasting impact on organisational performance.
Why is continuous improvement important?
Continuous improvement ensures that processes not only continue to function optimally, but can also respond effectively to changing circumstances. This could include new regulations, collaborative efforts, merger, or automation of processes. By integrating continuous improvement into transformation or change programmes, the organisation prevents obsolescence and remains agile and future-proof. McKinsey states, ‘For companies that embrace continuous improvement, eliminating costs is just a by-product of a much higher goal - empowering employees to work more efficiently and achieve growth through innovation in products and services.’
Committing to culture change
Successful implementation of continuous improvement often also requires a culture change within the organisation. Management plays a crucial role in this by actively supporting process management and clearly communicating its importance to all employees. Creating an open culture in which there is room for feedback and improvement encourages employees to take ownership and actively contribute to the improvement and success of processes.
In addition, it is important to involve diverse stakeholders. Involving cross-functional teams in mapping the AS-IS (current) situation helps to get a complete picture of how processes are currently running and where opportunities for improvement lie. By starting with simple adjustments, or the so-called ‘low hanging fruit’, employees quickly experience the positive effects of process-oriented thinking, which increases support for further changes.
Application of the DMAIC cycle
The DMAIC (Define, Measure, Analyse, Improve, Control) method helps to identify the root cause and solve problems from this perspective.
- Define: Identify and define the problem or improvement opportunity by focusing on activities that do not add value, or have a negative impact on costs, lead times or service quality. Areas for improvement can be identified by analysing the organisation and collecting feedback (both internally from employees and externally from customers/citizens).
- Measure: Map the AS-IS (current) situation by organising a process workshop with all stakeholders. Mapping this process will immediately reveal how processes currently function and where inefficiencies are.
- Analyse: In the analyse phase, you discover why problems arise in your process by verifying and validating possible causes based on facts. It is crucial to identify the real causes with accurate data so that you can develop and implement effective solutions. This will prevent the problem from recurring.
- Improve: Develop and implement solutions in collaboration with cross-functional teams, test them and refine where necessary to achieve the desired improvements. Include suggestions from process staff in this.
- Control: Secure the realised improvements and quality of service through standardisation, continuous monitoring and implementation of control / management measures to prevent relapse and encourage further optimisation.
The DMAIC cycle helps organisations to fully understand and optimise processes to focus on meeting customer quality requirements (CTQs), while minimising non-value-added activities.
Reviews and feedback
Establishing clear performance indicators and metrics is essential to assess the effectiveness of improvements. Assessments according to functional standards help organisations see how well their processes meet standards and where improvement is needed. Self-assessment by engaged employees is essential here, with a culture focused on improvement rather than perfection. This should be supported by feedback loops and benchmarking. Continuous improvement frameworks help organisations define their maturity level and set ambitious goals. Leadership plays a key role here, focusing on innovation, service redesign and digital transformation for better results.
How Engage Process supports a CI culture
The Engage Process platform offers various tools and functionalities to support a culture of continuous improvement:
- Going through processes together with executive staff, analysing them and mapping them gradually in Engage Process' Modeler (ideally as process workshop), allows you to capture and establish a baseline of your processes. Involvement of the operational staff is usually essential to properly map the processes, and especially the relevant exceptions. Intuitive, meaningful icons, drag & drop, Show/Hide ®, Switch View ® and a user-friendly interface provide an environment in which everyone can participate and help in modelling processes.
- During these process workshops, the platform provides real-time insight into the impact of proposed changes. By comparing AS-IS (current) and TO-BE (desired) processes, improvement opportunities quickly become visible and teams can immediately see the benefits of adjustments, contributing to People Driven Change.
- Departments such as the call centre for inbound queries and the finance department for invoices typically have ‘standard’ processes that are used within multiple other processes. Use process links in the Engage Process Modeler to integrate these standard processes into work processes (becoming “sub-processes”). When changes are made to this standard process, this means that the change only has to be made once.
- With the Value Stream View and bottleneck indicators, organisations can easily see which process steps add value and where bottlenecks exist. This not only helps you visualises current performance, but also helps teams to prioritise improvement initiatives.
- Lean principles suggest regular reviews and feedback sessions. In Engage Process, the feedback module can be used when a new or revamped process is implemented. With remote applications, there is capability for feedback from operational teams with the Viewer and recording suggestions that can be automatically incorporated via the brainstorming app.
Summary
Continuous improvement is an indispensable strategy for organisations that want to meet current demands and be prepared for future challenges. By investing in a culture of continuous improvement in which openness, commitment and feedback are central, organisations can operate in a more efficient, agile and effective manner.
Seeing is believing
Submit a form to start your 30 day trial. Easily map and analyse your processes to drive improvements across the organisation.
Student? Click here!